Decision Aids / TEX*A*Syst / Reducing Contamination by Improving Wellhead Management and Conditions
B.L. Harris, D.W. Hoffman and F.J. Mazac, Jr.
- Do you know the proper separation distances between a well and various possible water contamination sources, as well as other principles you should consider when choosing a water well site?
- Are you aware of the prominent subsurface geologic materials in your area?
- Does the casing in your well extend the recommended distance above the land surface and below the well water level?
- Is your well more than 40 years old?
- Has your well ever been inspected by a qualified well driller?
- Are you unsure of the type and depth of your well?
- Have you ever had your water well tested?
- Do you test your well at least once a year?
- Do you use anti-backflow devices when mixing pesticides, and on washing machines, pressure washers, swimming pools, etc. to prevent contamination of your water supply?
- Do you have any abandoned wells that are not properly capped and sealed?
If these questions create doubt about the safety of your management practices, this publication will provide helpful information.
Wellhead Management Background
About 95 percent of this country’s rural residents use ground water to supply their drinking water and homestead needs. Wells should be designed to provide clean, safe water. If improperly constructed or maintained, however, wells can allow bacteria, pesticides, fertilizer or oil products to contaminate ground water. These contaminants can put family and animal health at risk.
The condition of your well and its proximity to contamination sources determine the risk it poses to your ground water. For example, a cracked well casing may allow fertilizer, nitrates, oil or pesticides to enter the well if these materials are spilled near the well. Feedlots, animal yards, septic systems and waste storage areas also can release large amounts of bacteria, nitrates and other contaminants that could pollute well water.
The Texas Water Well Drillers Act (1985), the Water Well Pump Installer Act (1991) and various other legislative actions have guided development of regulations, primarily contained in Chapter 287 of the Texas Administrative Code, to provide for licensing of well drillers and pump installers and establish standards for drilling, capping and plugging water wells. For wells drilled before the effective date of current regulations (1983), well owners are responsible for ensuring that their wells do not contaminate ground water. Contact a licensed well driller or the Texas Natural Resources Conservation Commission for additional information.
Preventing ground water contamination is very important. Once ground water is contaminated, it is very difficult to restore it to its original condition. Most options are costly, and could involve treating the water, drilling a new well or obtaining water from another source. A contaminated well also can affect neighboring wells, posing a serious health threat to others.
A glossary at the end of this bulletin will clarify the terms used. This guide will cover the following areas of wellhead management:
- Well location
- Well construction
- Well age and type
- Well depth
- Maintaining existing wells
- Water testing
- New wells
- Unused and abandoned wells
Well Location
Whether a well taps water just below the ground or hundreds of feet deep, its surface location is a crucial safety factor. Locating a well in a safe place takes careful planning. Such factors as where the well is in relation to surface drainage, how the land is used, where chemical mixing and storage areas are located, and the direction of ground water flow must be considered. A well downhill from a livestock feeding facility, a leaking tank or a septic system has a greater risk of contamination than a well on the uphill side of these potential pollution sources.
Surface slope does not always indicate the direction a pollutant might flow once it gets into the ground. In shallow aquifers, ground water flow is often in the same direction as surface water flow. If the aquifer supplying water to your well is deep below the surface, though, its slope may be different than that of the land surface. Finding out about ground water movement on your property may require the use of special monitoring equipment installed and operated by trained personnel (see Contacts and References).
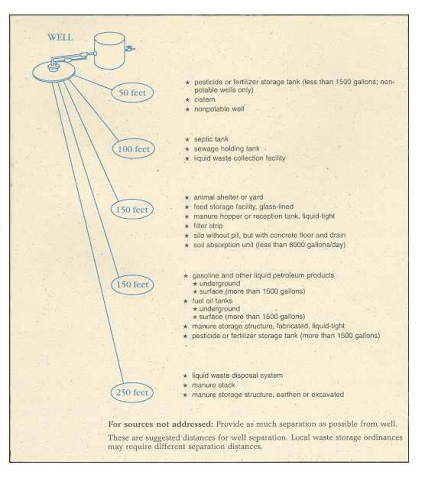
Figure 1. Minimum separation distances between well and potential farmstead sources of contamination for new well installation.
States encourage proper well location by requiring minimum separation distances from sources of potential pollution, thus using the natural protection provided by soil. Texas regulations for private water well drilling and construction (Texas Administrative Code NR 31, Chapter 287) provide guidelines for pesticide mixing, pesticide and fertilizer storage, vehicle maintenance, animal waste disposal, and other important activities. When no distances are specified, provide as much separation as possible between a well and any potential contamination source. This is especially necessary if your property is on highly permeable soils or thin soil overlying limestone bedrock, or if the contamination source or activity presents a high risk of contamination.
Minimum separation distances apply to new well installation in Texas (Fig. 1). Existing wells are required by law only to meet separation requirements in effect at the time the well was constructed. However, it is to your family’s benefit that you make every effort to exceed old requirements and meet current regulations whenever possible. Differences in soil and slope can make well siting an inexact science. Keep in mind that separation distances required by the State of Texas and some ground water districts are minimums. You may want to choose greater separation distances in some cases, depending on conditions at a particular site. For more information on the soil characteristics and geologic material of your well site, refer to those tables in B-6023, TEX*A*Syst Introduction.
Changing the location of a well in relation to contamination sources may protect your water supply, but not the ground water itself. Any condition likely to cause ground water contamination should be prevented, even if a well is far away from the potential source. Whether or not drinking water is affected, ground water contamination is a violation of Texas law (Texas Water Code Chapter 26). This law states that there shall be no lessening of ground water quality below the present quality.
Simply separating a well from a contamination source may reduce the chance of pollution, but it does not guarantee that the well will be safe. Wells located in the path of polluted water have a high risk of contamination from overland flow washing into an improperly sealed well.
Well Construction
Poor well design can cause ground water contamination by allowing precipitation and storm runoff to reach the water table without filtering through soil. Wells located in pits and wells without grout or caps can allow surface water to carry bacteria, pesticides, fertilizer or oil products into your drinking water supply. Proper well design and construction reduces the risk of pollution by sealing the well from anything that might enter from the surface.
Well characteristics important to proper well construction are described in the following sections. Information about the construction of existing wells may be available from the person who drilled the well, the previous owner or the well driller’s report. The Texas Natural Resources Conservation Commission can attempt to locate the driller’s report for you for a small fee.
Well Casing Slab and Cap
During construction the well driller installs a steel or plastic pipe called a casing to prevent collapse of the borehole. The space between the casing and the sides of the hole provides a direct channel for surface water (and pollutants) or ground water from undesirable aquifers to reach your drinking water. To seal that channel, the driller fills the space with grout (cement or concrete). Together, the grout and the casing prevent pollutants from seeping into the well (Fig. 2).
You can inspect the condition of a well casing at the surface by searching for holes or cracks. Use a light to check down the inside of the casing. If you can move the casing around by pushing against it, the casing probably fails to keep out contaminants. Also check the condition of the well casing by listening for water running down into the well when the pump is not running. If you do hear water, there could be a crack or hole in the casing, or the casing might not extend down to the water level in the well. Either situation may be risky.
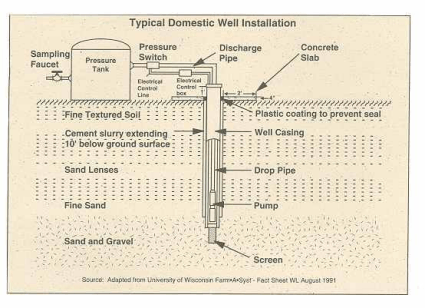
Figure 2. Typical domestic well installation with discharge pipe extending into the home.
A slab must be constructed around the casing at the ground surface. The slab must extend at least 2 feet from the well in all directions, be at least 4 inches thick, and slope away from the casing to drain water away from the well. In areas with high shrink-swell clays, the slab should be separated from the well casing by a plastic or mastic coating or sleeve to prevent bonding. The casing must extend at least 1 foot above the slab for most wells. If undesirable water is encountered in the drilling process, it must be sealed off to prevent contamination of other water.
To prevent contaminants from flowing down inside the well casing, the driller installs a tight fitting well cap that can’t be easily removed by children. The well cap should keep out insects, animals and surface water, but have a screened vent so that air can enter the well. Check the well cap to see that it is in place and tightly secured. Wiring should be in a conduit. If your well has a vent, be sure it faces the ground, is tightly connected to the well cap or seal, and is properly screened to keep out insects and animals.
Casing Depth and Height
The depth of casing required by the state private well code for any particular well depends on the nature of the subsurface geologic materials. Minimum requirements for unconsolidated formation wells (sand and gravel) are that casing should extend to a depth of 25 feet or 10 feet below the static water (water level in the well), whichever is deeper. Casing should extend to at least 30 feet for sandstone wells, and at least 40 feet for all other bedrock-type wells.
A well cased below the water level in the well provides greater protection from contamination because surface water is filtered through soil and geologic materials before entering the well. Typically, the casing extends 1 to 2 feet above surrounding land, preventing surface water from running down the casing or on top of the cap and into the well. The Texas Water Code requires that at least 12 inches of casing pipe extend above the top of the slab. The code also requires that the casing extend at least 2 feet above flood level.
Well Age and Type
Well age is an important factor in predicting the likelihood of contamination. A well constructed more than 50 years ago is likely to be near the center of the property; generally it is a relatively shallow well and is probably surrounded by many potential contamination sources. Older well pumps are more likely to leak lubricating oils, which can get into the well. Older wells also are more likely to have thinner casing that may be corroded through. Even modern casing in wells 30 to 40 years old is subject to corrosion and perforation. If you have an older well, you may want to have it inspected by a qualified well driller.
Dug wells pose the highest risk of drinking water contamination because they are shallow and often poorly protected from surface water. A dug well is a large-diameter hole, usually more than 2 feet wide, which is often constructed by hand.
Driven-point or sand point wells, which pose a moderate to high risk for contamination, are constructed by driving assembled lengths of pipe into the ground. These wells are normally smaller in diameter (2 inches or less) and less than 50 feet deep. This type of well can be installed only in areas of relatively loose soils, such as sand.
All other types of wells, including those constructed by a combination of jetting and driving, are drilled wells. Drilled wells for farm and homestead use are commonly 4 to 8 inches in diameter.
Well Depth
Shallow wells draw from the ground water nearest the land surface, which may be polluted by surrounding activities. Depending on how deeply the well casing extends below the surface, rain and surface water soaking into the soil may carry pollutants into the well bore.
Local geologic conditions determine how long it takes for this to happen. In some places, such as in karst terrain, this process happens quickly, in weeks, days or even hours. Areas with thin soil over fractured bedrock or sand and gravel aquifers are particularly vulnerable. Even sites with thick sands over bedrock are vulnerable to contamination. On the other hand, thick clay soils can slow the movement of contaminants to the water table.
Wells deeper than 100 feet are safer than shallow wells because the ground water supplying deep wells may have traveled a considerable distance underground over a long time, which filters contaminants.
Existing wells were most likely located according to traditional practices or regulations in place at the time of construction. While these wells are still legal, you may want to consider how the well conforms to current standards, which incorporate new knowledge about protecting ground water. These standards can be found in the Texas Administrative Code, Chapter 287.
Maintaining Existing Wells
Good maintenance means testing the water every year, keeping the well area clean and accessible, keeping pollutants as far away as possible and periodically (every few years) having a qualified well driller or pump installer check the well mechanics.
Older wells without proper casing, sealing and protective slabs, or with other problems, should be brought up to current standards for your own protection. Upgrade wells by getting rid of well pits, installing caps, extending casings, and moving such activities as pesticide mixing, tank rinsing or gasoline storage farther from your well. Almost all Texas property transfer forms include clauses about underground petroleum storage tanks and well water safety. If your well is in a storage shed or well house, do not store contaminants such as fuels or pesticides next to it. Do not winterize the well by wrapping pipes and pressure tanks with empty fertilizer or pesticide bags or other materials containing potential contaminants.
Pollution Source Management
It is expensive to change the location of some facilities such as livestock feeding areas or silos. Until you can meet minimum separation distance requirements, change the way you manage such structures to control contaminants.
If your silo is too close to your well, for example, you could install a system for collecting rainfall runoff draining from freshly ensiled forage. Likewise, you could install concrete curbs to direct livestock yard runoff away from the well.
Short-term stacks of wet manure can contaminate a well with bacteria and nitrates. Locate them 250 feet away from wells to reduce the chance of polluting your drinking water. Protect the stacks from rain to prevent leachate from entering the soil.
Other management changes you may want to consider include moving traffic areas and chemical or gasoline storage areas away from the well, and upgrading or managing the septic system.
Backflow Prevention
Backflow or back-siphoning from pesticide mixing tanks allows chemicals to flow back into the well through the hose. Use an anti-backflow device when filling pesticide sprayer tanks to prevent the chemical mixture from flowing back into the well and contaminating ground water. Inexpensive anti-backflow devices for hoses used to fill sprayers are available from irrigation and spray equipment suppliers and hardware stores. If you do not have such a device, keep the hose above the level of the liquid in the tank when filling the pesticide sprayer.
Consider purchasing an inexpensive plastic nurse tank. A nurse tank is filled with water at the well and then used to fill the sprayer away from the well. For more information about preventing well contamination from pesticide mixing and loading practices, see the TEX*A*Syst publication, B-6025 Reducing the Risk of Ground Water Contamination by Improving Pesticide Storage and Handling.
Water Testing
Keep an eye on water quality in existing wells by testing annually. Although you cannot have water tested for every possible pollutant, some basic tests can indicate whether or not a problem exists.
At a minimum, test water annually for bacteria and nitrates. Where the well draws from sandy materials or bedrock, testing at least once for corrosivity is also important. A good initial set of tests for a private well includes hardness, alkalinity, pH, conductivity and chloride. A visual interpretation of the water samples, as well as taste and odor tests, can provide valuable clues about possible contamination.
Test for contaminants that are most likely on your property. Test for lead if you have lead pipes or soldered copper joints, or are concerned about lead in the brass associated with a submersible pump (see Extension publication L-5096, Lead Contamination in Water Wells). Test for volatile organic compounds (VOCs) if there has been a nearby use, spill or production of oil, petroleum or solvent. While testing for pesticides can be very expensive (often $80 to $100 per compound analyzed), the expense may be justified if:
- a well has nitrate levels greater than 10 mg/l (reported as nitrate-nitrogen, NO3-N) or 45 mg/l (reported as nitrate, NO3);
- a pesticide spill has occurred near the well or back-siphonage has occurred;
- a well is shallow, with less than 15 feet of casing below the water table; or
- a well is located in sandy soil and down-slope from irrigated croplands where pesticides are used.
For more information on appropriate tests to run, contact your county Extension office, health department, ground water conservation district, or the Texas Natural Resource Conservation Commission.
Test well water if any of the following occur:
- a notable change in water taste, odor, color or clarity;
- an unexplained illness in the family;
- a pregnancy in the family;
- any noticeable changes in livestock or poultry performance;
- neighbors find a particular contaminant in their water;
- a spill or back-siphonage of chemicals or petroleum products near a well or near your home;
- chemical or manure application to fields within 100 feet of a well;
- livestock operation inspectors require it;
- landfills or changes in land use nearby; or
- a new well is drilled.
You can have water tested by both public and private laboratories. A list of certified labs is available from the Texas Natural Resource Conservation Commission and the Texas Agricultural Extension Service Soil and Water Laboratory.
Follow the lab’s instructions for water sampling to ensure accuracy of results. Use only the container provided and return samples promptly. Bacteria sample bottles are sterile and must be returned within specified time limits.
It is also important to record test results and to note changes in water quality over time. In addition to water analysis test results, you should keep records on well construction details, water levels and dates, and maintenance intervals for the well and pump.
New Wells
New wells are expensive, but they are a good investment for the future. Getting the most from such an investment means locating the well away from contamination sources and working to maintain the quality of the well. Here are some simple principles to follow:
- Follow the state recommended minimum separation distances. Texas law states these separation distances and other requirements for drinking water wells. A full listing is also available from your county Extension office, the Texas Natural Resource Conservation Commission, or a well driller.
- Locate your well on ground higher than surrounding pollution sources such as fuel tanks, livestock yards, septic systems or pesticide mixing areas.
- Construct a concrete pad around the well so that all surface water drains away from it, as required by law.
- Avoid areas that are prone to flooding.
- Locate the well so that pollution sources are downslope from the well. Ground water generally flows from upland areas and discharges into a surface water body.
- Make the well accessible for pump repair, cleaning, testing and inspection.
- Hire a competent, licensed well driller and pump installer. Make sure the driller disinfects the well with chlorine after construction, tests the water for bacteria after drilling, and provides you with detailed information about the well’s depth and construction.
Unused and Abandoned Wells
Many farms and ranches have unused wells. Wells at old home sites or old windmills are common. No one knows how many of these wells there are in Texas, although estimates range into the tens of thousands. Sources of information on well locations include the Texas Water Development Board, the Texas Natural Resource Conservation Commission, underground water conservation districts, and licensed water well drillers.
If not properly plugged, these abandoned or unused wells can provide a direct conduit for surface water carrying pollutants to ground water, or these abandoned wells can allow contaminants to move from one aquifer to another. One improperly sealed well in Texas was buried with only a stone covering the top of the casing. This well caused severely contaminated drinking water to be pumped from another well on the same property. The unused well was near a livestock corral and a septic tank. It allowed animal waste to directly enter the ground water. Just as unused wells pose a threat to ground water, large open wells pose safety hazards for small children and animals.
Everyone remembers the baby Jessica incident in which a young girl playing in her backyard fell into an abandoned well. Hire a licensed, registered well driller or pump installer to close old wells, since effective well plugging calls for experience with well construction materials and methods, as well as a working knowledge of the geology of the well site. You may, however, do your own well abandonment work. A license is not required, but you must meet the minimum well code requirements when you abandon and fill a well.
Regulations in Texas Water Codes provide guidelines for properly plugging abandoned wells. Special equipment is often required to remove old pumps and piping and to properly install sealing material inside the well. Use of inappropriate materials and methods can lead to well settling, collapse and potential ground water contamination. If plugging materials are improperly installed in a well, patching up defective work is nearly impossible.
Pipes sticking out of the ground or under an old windmill are the most obvious ways to locate unused wells. You may not know the history of your property, and unused well locations may not be obvious. A depression in the ground may indicate an old well. Also, wells were often drilled in basements of houses, under front steps, and near old cisterns.
State regulations require that plugged wells be reported, and that the following be done:
- Remove the pump, piping, and any other obstructions from the well.
- Chlorinate the well before it is sealed. The entire length of the well should then be sealed with slurries of cement or clay to prevent surface water from entering the ground water and to prevent contaminant movement from one aquifer to another.
- Restore as closely as possible the geologic conditions that existed before the well was constructed. For specific requirements, consult the Texas Natural Resource Conservation Commission well abandonment brochure (see Contacts and References) or the well code.
Proper well closing takes time and money. Costs will vary with the well depth, diameter and the geology of the area. Spending a few hundred dollars plugging an unused well near your home may prevent contamination of your drinking water.
Evaluation Table
The following table can be used to help agricultural producers and rural homeowners determine the risk that drinking water on a given property will be contaminated by the management practices being used. For each category on the left, read across to the right and circle the statement that best describes conditions on your land. Allow 15 to 30 minutes to complete the worksheet, and skip any categories that do not apply. Note any high risk ratings and take appropriate actions to remedy them. Strive for all low or low to moderate risk ratings.
Drinking Water Well Condition: Assessing Drinking Water Contamination Risk
Glossary
Abandoned well: A well that has not been used for 6 consecutive months and is capped and not deteriorated.
Air gap: An air space (open space) between the hose or faucet and liquid level, representing one way to prevent backflow of liquids into a well or water supply.
Anti-backflow (anti-back-siphoning) device: A check valve or other mechanical device to prevent unwanted reverse flow of liquids back down a water supply pipe into a well.
Aquifer: A stratum or zone beneath the surface of the earth capable of producing water, as from a well.
Backflow: The unwanted reverse flow of liquids in a piping system.
Back-siphonage: Backflow caused by formation of a vacuum in a water supply pipe.
Capped well: Well covered with a cap that prevents surface pollutants from entering the well and that can sustain at least 400 pounds.
Casing: Steel or plastic pipe installed while drilling a well to prevent collapse of the well bore hole and entrance of contaminants, and to allow placement of a pump or pumping equipment.
Cross-connection: A link or channel between pipes, wells, fixtures or tanks carrying chemical solutions or contaminated water and those carrying potable (safe for drinking) water. Contaminated water, if at higher pressure, can enter the potable water system.
Drilled wells: Wells not dug or driven, including those constructed by a combination of jetting or driving. Domestic wells are normally 4 to 8 inches in diameter.
Driven-point (sand point) wells: Wells constructed by driving assembled lengths of pipe into the ground with percussion equipment or by hand. These wells are usually smaller in diameter (2 inches or less), less than 50 feet deep and can be installed in areas of relatively loose soils, such as sand.
Dug wells: Large-diameter wells often constructed by hand.
Ground water: Subsurface water in an aquifer.
Grout: Slurry of cement or clay used to seal the space between the outside of the well casing and the bore hole, or to seal an abandoned well.
Milligrams per liter (mg/l): The weight of a substance measured in milligrams contained in one liter. One mg/l is equivalent to 1 part per million in water measure.
Parts per million (ppm): A measurement of concentration of one unit of material dispersed in one million units of another.
Water table: The upper level of ground water in a zone of saturation. It fluctuates with climatic conditions on the land surface and with aquifer discharge and recharge rates.
Well cap (seal): A device used to cover the top of a well casing pipe.
Well plugging: An absolute sealing of the well bore.
Contacts and References
General information concerning ground water flow direction and water quality can be obtained from:
- Texas Water Development Board Ground Water Data Unit at (512) 445-1484, Office of Water Resources Management,
- TNRCC Agricultural Division Water Well Drillers Team Environmental Assessment, Division Ground Water Protection,
- Office of Administration Information Resources, Customer Service for Drillers’ Reports.