Decision Aids / TEX*A*Syst / Reducing Contamination by Improving Petroleum Product Storage
B.L. Harris, D.W. Hoffman and F.J. Mazac, Jr.
- Do your store liquid petroleum products closer than 100 feet from your water well?
- Are you planning to build a new petroleum storage tank on your property?
- Do you store petroleum products below ground on your property?
- Does your storage system lack proper spill and overfill protection?
- Do you store petroleum products in an above-ground tank?
- Is your tank more than 20 years old?
- Do you need to become more aware of proper petroleum tank monitoring procedures?
- Do you have any storage tanks that are no longer in use?
If these questions create doubt about the safety of your management practices, this publication will provide helpful information.
Petroleum Products Overview
Storing liquid petroleum products, such as motor fuel and heating fuel, above ground or underground presents a potential threat to public health and the environment. Nearly one out of every four underground storage tanks in the United States may now be leaking, according to the U.S. Environmental Protection Agency. If an underground petroleum tank is more than 20 years old, and especially if it is not protected against corrosion, the potential for leaking increases dramatically. Newer tanks and piping can leak, too, especially if they were not installed properly.
Even a small gasoline leak of one drop per second can result in the release of about 400 gallons of gasoline per year. A few quarts of gasoline in the ground water may be enough to severely pollute drinking water. At low levels of contamination, fuel contaminants in water cannot be detected by smell or taste, yet seemingly pure water may be contaminated to the point of affecting human health.
Preventing tank spills and leaks is especially important because gasoline, diesel and fuel oil can move rapidly through surface layers and into ground water. Also, vapors from an underground leak that collect in basements, sumps or other underground structures have the potential to explode.
Petroleum fuels contain a number of potentially toxic compounds, including common solvents such as benzene, toluene and xylene, as well as additives such as ethylene dibromide (EDB) and organic lead compounds. EDB is a carcinogen, a cancer-causing agent, in laboratory animals, and benzene is considered a human carcinogen.
This publication focuses on safe storage of gasoline, diesel, kerosene and liquid heating fuels. It does not apply to liquid propane (LP) gas, since such leaks vaporize quickly and do not threaten ground water. A glossary at the back of this publication explains the terminology used. The following areas are covered:
- Storage tank location
- Tank design and installation
- Monitoring tanks
- Tank closure
- Evaluation table
Storage Tank Location
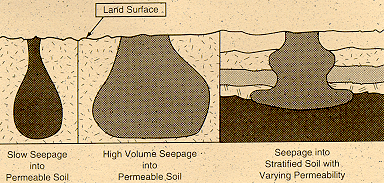
Figure 1. Petroleum product seepage into soils. Source: Underground Tank Corrective Action Technologies, EPA/625/6-87-015, January 1987.
From a water quality standpoint, one of the most important aspects of your liquid petroleum storage tank location is how close it is to your water well. State well regulations require that petroleum storage tanks be at least 100 feet from a water well. Minimum separation distances regulate only new well installation. Existing wells are required by law only to meet separation requirements in effect at the time of well construction. However, making every effort to meet current regulations whenever possible will further reduce the risk of contamination.
Every site has unique geologic and hydrologic conditions that affect ground water movement. The time it takes petroleum products to reach ground water also will depend upon local soils. The more porous the soil (sands and gravels, for example), the faster the rate of downward movement to ground water. You may choose to locate a new tank more than 100 feet away from a well to provide reasonable assurance that subsurface flow or seepage of contaminated ground water will not reach the well. If possible, the tank should be located down-slope from the well. Figure 1 illustrates petroleum product seepage into soils.
If you have an above-ground tank, follow existing regulations for underground storage tanks as a guide. To protect against explosion and fire, do not locate tanks (especially above-ground tanks) closer than 25 feet to existing buildings. Previous regulations for siting above-ground storage tanks were concerned more with the danger of explosion than with the danger of ground water pollution. State agencies have revised above-ground storage tank regulations to better protect ground water. However, always keep in mind the potential for vapors to accumulate in or under nearby storage buildings. These vapors can directly affect human health and are a fire hazard.
Along with maintaining adequate distance from your drinking water well, choose a location for a new tank based on the following considerations:
- Soil characteristics. Highly corrosive clays, wet soils and acidic (low pH) soils can significantly increase the rate of corrosion of underground metal tanks and piping. Use clean backfill during installation to decrease the negative effects of surrounding soils.
- Soil stability. Assess the suitability of the underlying soil to support both underground and above-ground tanks. At special tank locations, such as hillsides, be sure to properly anchor and hold tanks in place. Regardless of soil conditions, locate above-ground tanks over an impermeable liner made of concrete or one of the newer synthetic fabrics and build a collection basin for spills.
- Damage control. Be sure that pipes cannot twist or break if the tank is bumped or disturbed.
- Current and previous land use. Sites that contain abandoned pipes and tanks, agricultural drainage tiles or waste materials pose special installation problems. Any metal already in the ground at your chosen site will increase corrosion rates for the new tank.
- Traffic. Assess traffic patterns around the tank. Determine whether the location of the tank or dispenser will block movement of vehicles during refueling or cause special problems if any work needs to be done on the tank. Protect piping from collisions with vehicles.
- Depth to ground water. Floodways or areas where the water table is close to the surface are poor locations for storage tanks. Tanks placed in such areas require special installation. To reduce pollution potential, an above-ground tank may be preferable to an underground tank in some situations.
Tank Design and Installation
Whenever you install a fuel storage tank, carefully follow the manufacturer’s recommended installation practices. Proper installation is one sure way to minimize leaks from the tank or connected piping. Scratches in a metal tank caused by careless installation can increase corrosion and tank deterioration.
Underground Tanks
All new underground petroleum storage tanks and related piping must be constructed of non-metallic materials, such as fiberglass, or have corrosion protection. Methods of corrosion protection include using interior liners and sacrificial anodes which are connected to the tank.
A sacrificial anode is a special material with a greater tendency to corrode than the tank material. The anode will typically protect the tank for up to 30 years. Interior liners are made of non-corrosive synthetic materials and also can be effective in protecting metal tanks.
Texas regulations require that all new underground tanks (other than heating oil tanks for on-site use) have spill and overfill protection. Spill protection typically consists of a catch basin for collecting spills when the tank is filled. Overfill protection is either a warning device, such as, a buzzer or a prevention device such as an automatic shutoff. Spill and overfill protection are important because they can prevent pollution from a number of small releases over a long period of time.
Above-ground Tanks
State regulations for above-ground tank installation seek to reduce the potential for both pollution and fire. Requirements include the following:
- enclosing the tank within a secure 6-foot fence or well-ventilated building constructed of non-combustible material; and
- constructing a fire wall between the fuel dispensing area and the tank.
To decrease pollution potential, place tanks within a secondary containment structure consisting of a dike and a pad. All piping should be above ground within the dike or may go over the dike wall. However, if it goes over the dike wall, it must be placed below the ground and within 10 feet of the dike wall. Above-ground piping must be made of steel and coated to prevent corrosion. Any below-ground piping may be either steel or fiberglass, but the steel piping must be coated and cathodically protected.
Monitoring Tanks
Regulations for new underground tanks require that they have a method of detecting leaks. Select the tank location carefully to ensure that installation is easy and leak detection methods reliable. Test the tank periodically for leaks, and measure the tank inventory on a monthly (or more frequent) basis to help detect leaks before major problems develop.
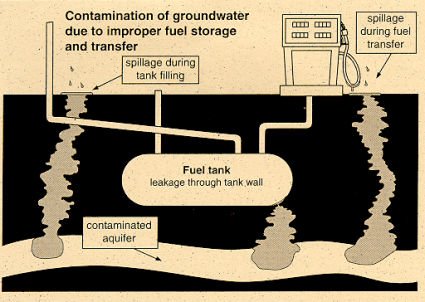
Figure 2. Contamination of groundwater due to improper fuel storage and transfer. Source: Handling and Underground Storage of Fuels, Cooperative Extension Service, Michigan State University, Extension Publication WQ01, Reprinted, February 1986.
Since cleanup of gasoline leaks is always costly and often not totally effective, it is important to constantly monitor underground tanks containing petroleum products. If you already have a petroleum storage tank, be especially aware of the age of your tank as well as the need to establish a leak-detecting program. Figure 2 shows how ground water can be contaminated by underground tanks.
Since most older tanks are bare steel, they are likely to corrode and leak. If your tank is more than 20 years old or if you do not know its age, make a special effort immediately to determine whether there are leaks.
Even when a tank has been tested and proven tight, existing regulations and good practice require that you have a method for regularly detecting leaks. Some good methods include the following:
- Installing internal or external devices to monitor ground water and vapor, or to automatically gauge tanks.
- Measuring tank inventories regularly. Leak-age is apparent when there is any decrease in level over time, without any withdrawal of fuel, or when there is an increase in water in the tank. While inventory measurement will not detect very small leaks, it will at least provide a warning that further investigation may be necessary.
- Using a measuring stick to measure tank liquid level. This method is acceptable, but be sure that the stick does not puncture or damage the bottom of the tank.
The closer the tank is to a water well, the more important it is to have an adequate leak detection system in place.
Tank Closure
Tanks no longer in use can cause problems for owners and operators many years later. They will continue to corrode and, if they still contain gas or oil, will likely contaminate ground water.
Try to determine the location of any unused tanks on your property. Also, try to find out whether the tanks still hold product or have holes. These tanks must be pulled from the ground and disposed of in a landfill or at a scrap dealer.
State law requires that only certified individuals can legally pull a tank. Always notify your local fire department at least 1 month before you have the tank pulled so that they can take precautions to prevent an explosion or other problem. Deaths have occurred because of improper closure.
Evaluation Table
The following table can be used to help agricultural producers and rural homeowners determine the risk that drinking water on a given property will be contaminated because of the management practices being used. For each category on the left that is appropriate, read across to the right and circle the statement that best describes conditions on your land. Allows 15 to 30 minutes to complete the table, and skip any categories that do not apply. Note any high risk ratings and take appropriate actions to remedy them. Strive for all low or low-moderate risk ratings.
Petroleum Product Storage: Assessing Drinking Water Contamination Risk
Glossary
Cathodic protection: One of several techniques to prevent corrosion of a metal surface by reversing the electric current that causes corrosion. A tank system can be protected by sacrificial anodes or impressed current (See sacrificial anodes and impressed current.).
Certified installer: A person certified by the state to install and repair petroleum storage tanks.
Corrosion: Deterioration of a metallic material due to a reaction with its environment. Damage to tanks by corrosion is caused when a metal underground tank and its underground surroundings act like a battery. Part of the tank can become negatively charged and another part positively charged. Moisture in the soil provides the connecting link that finally turns on these tank batteries. Then, the negatively charged part of the underground tank system where the current exits from the tank or its piping begins to deteriorate. As electric current passes through this part, the hard metal begins to turn soft, holes form and leaks begin.
Corrosion protection: One method of corrosion protection is cathodic protection. Steel tanks can be protected by coating them with a corrosion-resistant material combined with ‘cathodic’ protection. Steel underground tanks also can be protected from corrosion if they are bonded to a thick layer of noncorrosive material, such as fiberglass-reinforced plastic. Also, the corrosion problem can be entirely avoided by using tanks and piping made completely of noncorrosive material, such as fiberglass.
Galvanized: The result of coating an iron or steel structure with zinc. Galvanized materials do not meet corrosion protection requirements.
Impressed current: This protection system introduces an electric current into the ground through a series of anodes that are not attached to the underground tank. Because the electric current flowing from these anodes to the tank system is greater than the corrosive current attempting to flow from it, the underground tank is protected from corrosion.
Interior liner: A liner for petroleum storage tanks made of noncorrosive synthetic materials that can be effective in protecting metal tanks.
Inventory control: Measuring and comparing the volume of tank contents regularly with product delivery and withdrawal records to help detect leaks before major problems develop.
Sacrificial anodes: Pieces of metal attached directly to an underground tank that are more electrically active than the steel tank. Because the anodes are more active, electric current runs from the anodes rather than from the tank. The tank becomes the cathode (positive electrode) and is protected from corrosion. The attached anode (negative electrode) is sacrificed or consumed in the corrosion process.
Secondary containment: A system such as a sealed basin and dike that will catch and hold the contents of a tank if it leaks or ruptures.
Soil permeability: The quality that enables soil to transmit water, air or other fluids. Slowly permeable soils have fine-textured materials, such as clays, that permit only slow fluid movement. Moderately or highly permeable soils have coarse-textured materials, such as sands, that permit rapid fluid movement.
Spill and overfill protection: Spill protection usually consists of a catch basin for collecting spills when the tank is filled. Overfill protection is a warning device such as a buzzer or a prevention device such as an automatic shutoff. These precautions can prevent a number of small releases over time from polluting ground water.
Tank tightness testing: A procedure for testing a tank’s ability to prevent the leaking of any stored substance into the environment, and to prevent ground water from seeping into the tank.
Contacts and References
For additional information, contact your county Extension agent or Texas Natural Resources Conservation Commission office.